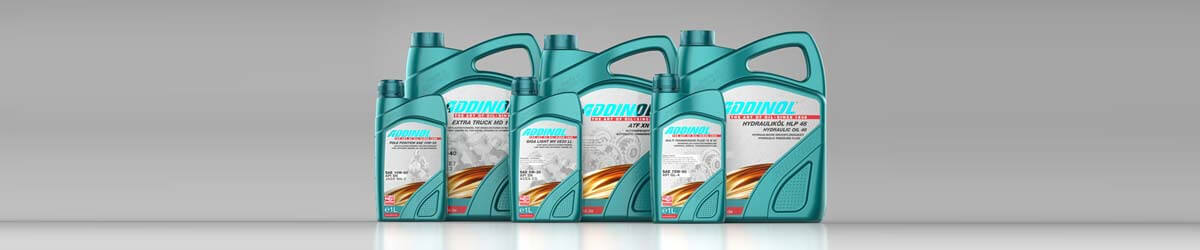

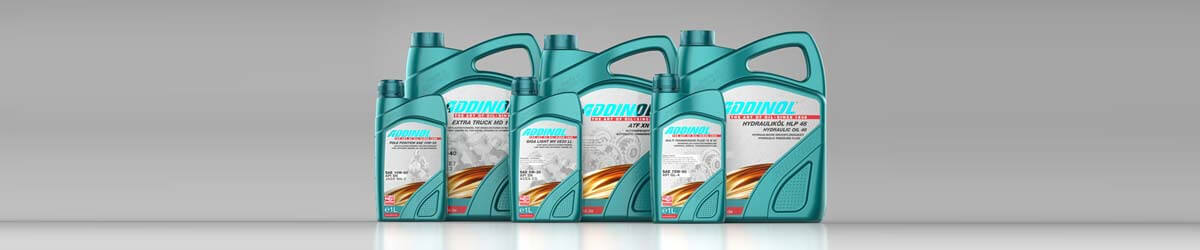
Micropitting on gears
Micro-pitting is the term used to describe the smallest cracks and material chipping on metallic components. It is a fatigue damage that causes cracks to form in the near-surface microstructure area as a result of disruption. The so-called micropittings are so small that they are only perceived as matt grey spots on the surface of the material. Only under strong microscopic magnification the material breakouts can be detected.
The pitting can be a consequential damage of the micro-pitting, which causes larger breakouts at the friction partners.
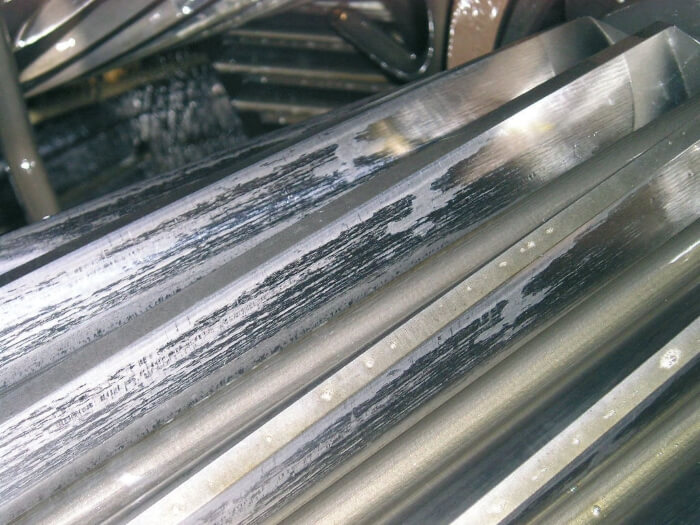
Causes of micropitting
Micro-pitting occurs primarily with low lubricant film thicknesses or rough surfaces combined with high surface pressures in surface-hardened flanks or running surfaces. Mixed and sliding friction occurs, which deforms the surface with microcracks. Gears, camshafts and rolling bearings are often affected by wear if the friction partners interact with each other under particularly high pressure. Usually, lubricants with insufficient EP properties (extreme pressure) are usually used. The load carrying capacity of the gear oil is therefore too low to permanently separate the friction partners from each other.
The following circumstances favour micropitting:
- High pressure produces more friction
- High temperatures in the system cause a thin lubricating film
- Roughened material requires a thicker lubricating film
- Use of lubricants with inadequate or incorrect additives
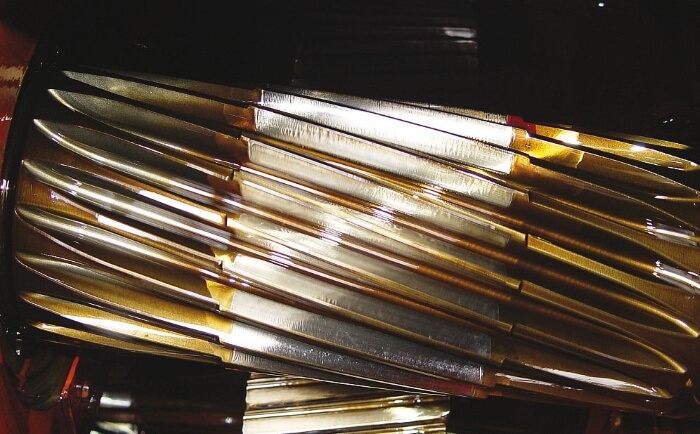
Problems due to micropitting
Even if the micropittings do not yet represent an extreme damage pattern, the microcracks can already hint at changes in the system. For example, micro-pitting can change the flank shape of gears and cause a drop in the performance of the system. This applies above all to industrial plants such as mill drives, rolling mills or wind turbines. In addition, there may be noise development in the gear unit, which you should always take as an indication to check the condition of the system.
If the micro-pitting remains untreated, the initially slight damage pattern soon develops into larger break-outs, which in the long run lead to a total loss including a gearbox change. But that doesn't have to happen.
Prevention of micropitting
Since industrial gear units or rolling mills are naturally subject to high pressure and the conditions for a functioning plant are usually accompanied by extreme demands on the material, micro-pitting can only be prevented with the right lubricant. The best possible separation of the friction partners prevents wear and material damage.
Therefore, always choose a lubricant with sufficient micro-pitting resistance and an additive reserve against long-term fatigue. These include the ADDIONOL Eco Gear 220 M, for example. In the FLENDER gray spot test, our gear oil has reached the "high" load-bearing class. This confirms that the formation of micro-pitting can practically be completely ruled out with using the oil.
Gear oils against micropittings
The right oils help against micro-pitting on gearboxes. The ADDINOL Eco Gear series have been specially developed to prevent micropitting on gearboxes, to smooth in micropitting and to repair already existing damage. We recommend the series Gear Oil F, Eco Gear M and Eco Gear S. The gear oils are available in different viscosity classes and are therefore suitable for many manufacturer approvals. Let us advise you in case of ambiguities.
ADDINOL GEAR OIL 220 F
Specifications / Approvals:
DIN 51517-3 (CLP), ISO 12925-1, AGMA 9005-E02, Siemens MD (Flender Rev. 15)
ADDINOL ECO GEAR 220 M
Specifications / Approvals:
DIN 51517-3 (CLP), ISO 12925-1
erfüllt die Anforderungen an:
Flender
ADDINOL ECO GEAR 220 S
Specifications / Approvals:
DIN 51517-3 (CLP), ISO 12925-1, AGMA 9005-E02
erfüllt die Anforderungen an:
Flender
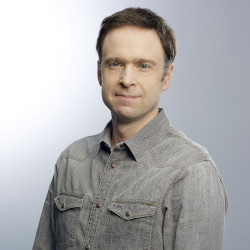