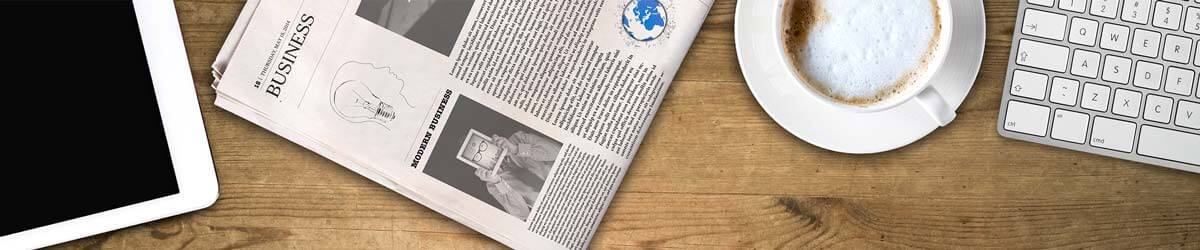

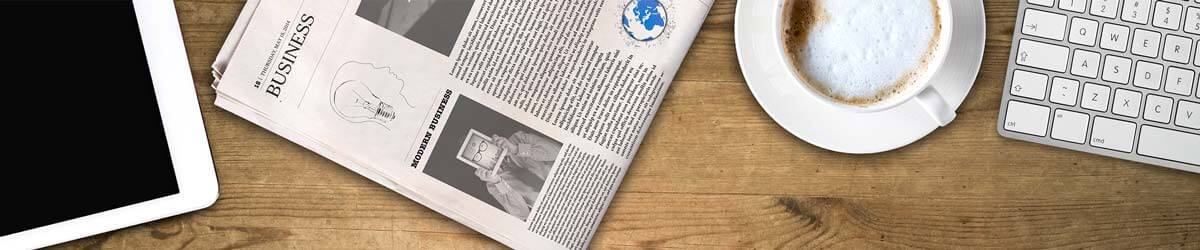
Successful application of ADDINOL Belt Lube HT products
Best Practice: Wood processing industry,
continuously working press lines
Press lines place high requirements on the lubricants used at belts, bending and rolling rods as well as chains. During manufacturing temperatures achieve peaks between +240 and +255 °C, belt speed is up to 90 m/min, pressures can reach 600 N/mm². In addition, wood-processing plants generally work at a dusty, humid and chemically aggressive environment (glues, release agents). Typically, such plants operate at constantly high temperatures bearing the risk of lubricant residues, cracking and incrustations on chain components, rods, belts and rollers. These might hinder the smooth run of belt, bending rods and chain and quickly can cause a standstill of the whole plant.
Best Practice: Successfully changeover of Dieffenbacher press line in Shangdong, China
The use of ADDINOL Belt Lube HT lubricants at the Shandong site in China has proven to be worthwhile for our customer. Two production lines were selected, their belt drive filled with ADDINOL Belt Lube HT 220 and their chain drive filled with ADDINOL Belt Lube HT 100 and closely monitored by the service company on site. Production parameters such as chipboard thickness and speed of the press line ensured the comparability of the operating conditions so that the consumption data before and after the oil change could be documented.
Drastic reduction of energy and oil consumption
Because of the tailored selection of special base components the lubricants of the ADDINOL Belt Lube HT range display optimum lubricating film thickness for high-speed plants under highest loads and temperatures. This way an improved rolling movement of all components is possible. Because of its powerful additivation the ADDINOL Belt Lube HT range possesses outstanding friction coefficients compared to competitive products. A lower frictional resistance produces reduced thermal and mechanical loads on the components involved having positive effects on the operating life of the whole plant. At the same time, efficiency is improved and less energy input is required for driving the chains.
After changeover to ADDINOL Belt Lube HT 220, a reduction in energy consumption of up to 23% was achieved under comparable operating conditions for both lines. The same could be reached for the oil consumption of both lines: up to 33% less oil consumption on the belt with ADDINOL Belt Lube HT 220 and up to 21% less oil consumption on the chains due to the changeover to ADDINOL Belt Lube HT 100.
Each plant has to be considered individually. In order to make the most of the benefits of the Belt Lube HT range it might be necessary to adjust lubricant supply. When changing over to ADDINOL Belt Lube HT central lubrication systems, as well as lubricant and energy consumption should be monitored. Only if considering all factors the efficiency increase can be proven.
With the proper use of ADDINOL Belt Lube HT 220 and HT 100, Dieffenbacher was able to reduce costs for maintenance and repair of their continuous working press lines. On the other hand, expenses for operating materials such as the lubricant itself as well as the energy for driving the press lines could be scaled down to a considerable extent. These are outcomes also resulting in a long-term increase in plant availability and lower reinvestments.
The right product for each application
ADDINOL Belt Lube HT 220, HT 100 and HT 50:
- Belt Lube HT 220 preferred for steel bands and rollers at continuous systems of Dieffenbacher and Siempelkamp as well as conveyor systems in discontinuous Küsters press lines
- Belt Lube HT 100 ideal for chains and bending rods in Dieffenbacher presses as well as rollers in Siempelkamp systems
- Belt Lube HT 50 useable for the lubrication of bending rods in older systems of Dieffenbacher, suited also for older Siempelkamp or Küsters presses
- conveying and distributing by the help of central lubrication systems, application by drop oiler and sprayer